
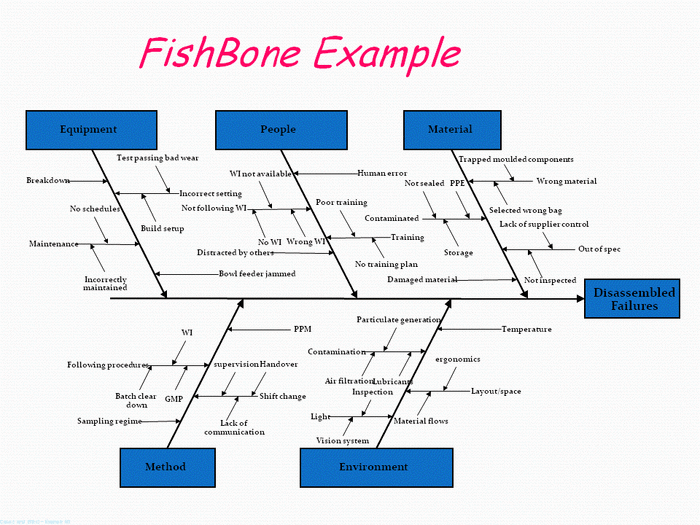
Measurements: How is the process measure and monitor to evaluate quality?.
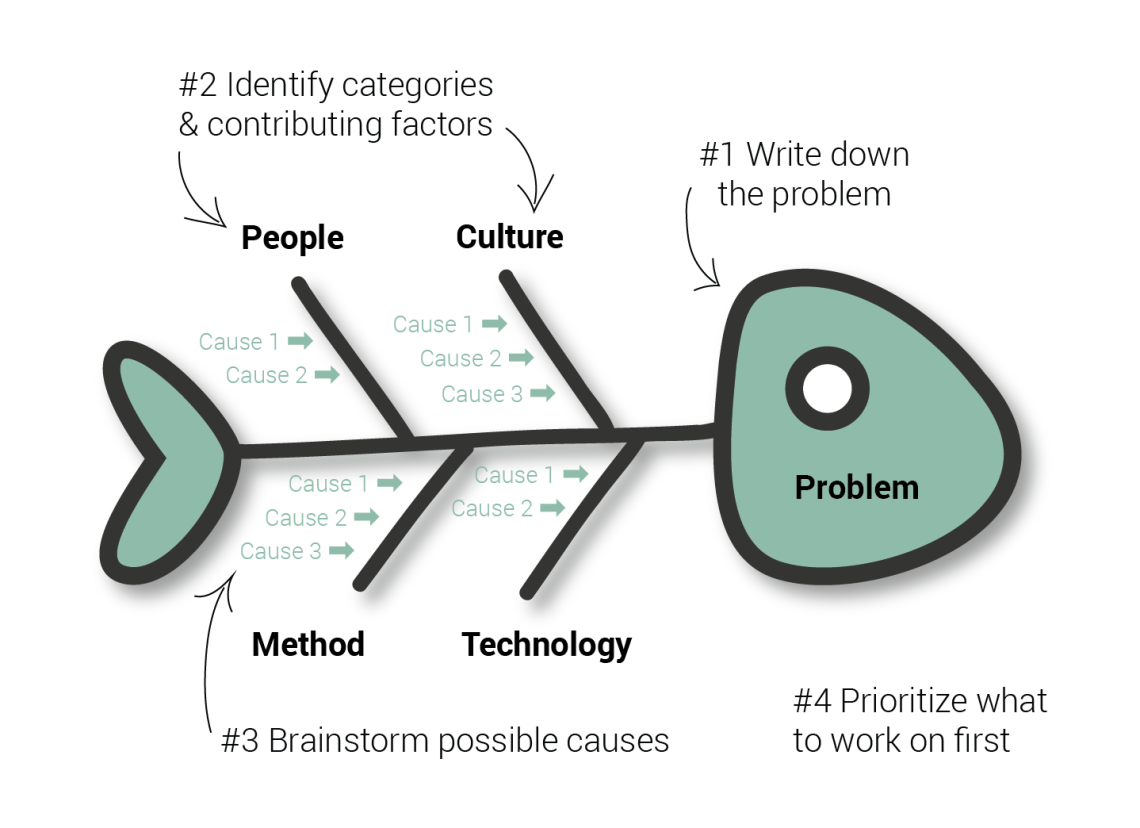
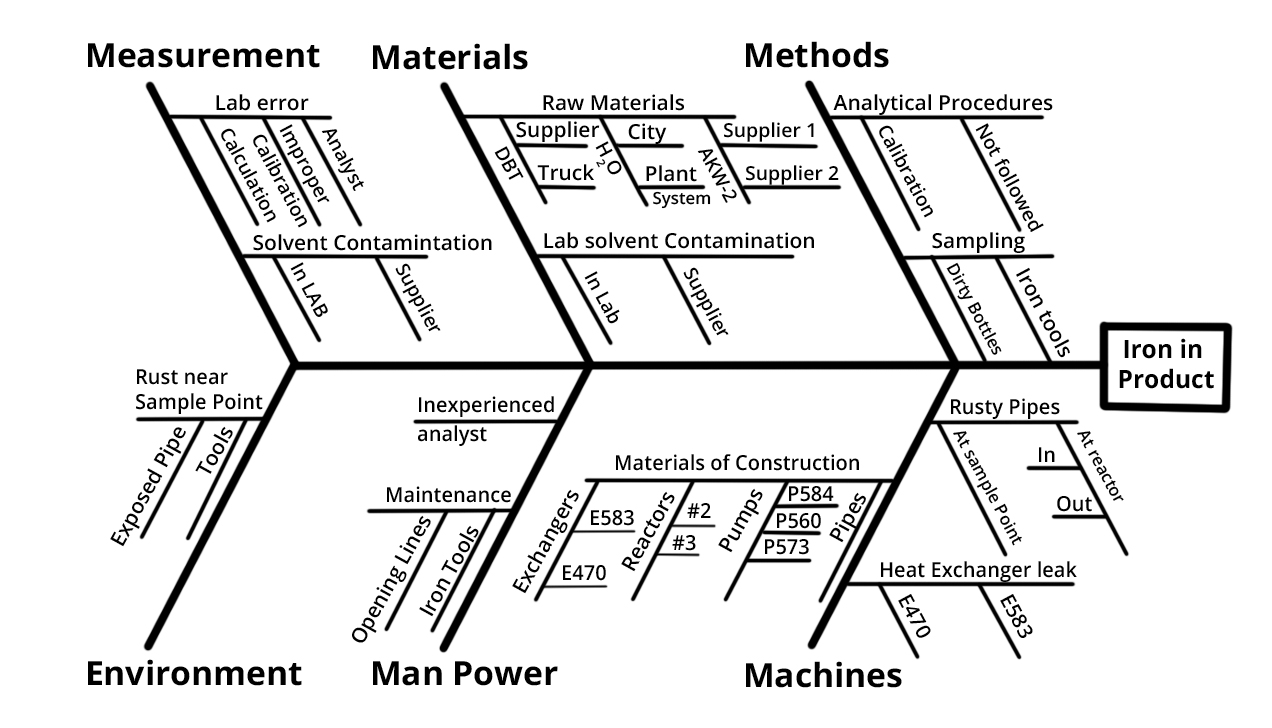

#Ishikawa diagram definition software#
Professional diagramming software may help creating Fishbone (Cause and Effect or Ishikawa) diagrams. Ishikawa fishbone diagrams can be use by most of the entrepreneurs and almost any industry or person having a problem. The Ishikawa fishbone diagram strives to pinpoint everything that’s wrong with current market offerings so that you can develop an innovation that does not have these problems.
#Ishikawa diagram definition how to#
They allow you to make your plans so that you know how to deal with them in such a way that the quality of your final product is still up to standard and without significant variation. Ishikawa fishbone diagrams help you to determine the variables that may enter the equation. Variation in the process means variation in the product. Whatever your business is, you do not want to leave anything up to chance.įrom the moment your client contacts you, a predictable process should follow with its aim being complete customer satisfaction. When it comes to quality and efficiency, variation is our enemy. The iconic Mazda Miata car was design to overcome the issues identify in an Ishikawa fishbone diagram. The Ishikawa Fishbone diagram was develop by Kaoru Ishikawa during the 1960s as a way of measuring quality control processes in the shipbuilding industry. It shows where quality control issues might arise and determine which resources are require at specific times. It is a diagram that shows the causes of an event and is often use in manufacturing and product development to outline the different steps in a process. These are use in the “analyze” phase of Six Sigma’s DMAIC (define, measure, analyze, improve, control) approach to problem solving. Ishikawa fishbone diagrams are consider one of the seven basic quality tools. He credit for inventing the fishbone diagram for helping employees avoid solutions that address only the symptoms of a much larger problem. Kaoru Ishikawa was a Japanese quality control expert. Ishikawa fishbone diagrams are normally work right to left.Įach large “bone” of the fish branch out to include the smaller bones containing more details.ĭr. The design of diagram resembles skeleton of a fish. Once the team brainstorm all the possible reasons for a problem, the facilitator helps team rating the probable causes according to their level of importance and diagram a hierarchy. Although, fishbone diagram combines brainstorming with a type of mind map template.Īdditionally, the diagram is helpful in troubleshooting processes and product development. Ishikawa fishbone diagram is typically use for the root cause analysis. Is fishbone diagram effective in finding potential causes? How many types of fishbone diagrams are there? Question: Why there was moisture in the atmosphere?.Fishbone Diagram Example 1: ABC Manufacturing Pvt.A step-by-step guide to find the causes:.And some Service industries use the 5Ss:.A few marketing industries use the categories as 7Ps:.The 6 general categories of analysis are:.Post Graduate Program in Content Writing.Find our Upcoming Batches of Six Sigma Green Belt Certificate :.Lean Six Sigma Green Belt Certification Training.This article will help you with all you need to know about Fishbone Diagram in 2023. This visual cause-and-effect analysis tool assists you in identifying the various reasons for a problem in your quality control chain, allowing you to address and resolve issues at their source. Consider using a Fishbone diagram the next time you undertake an internal company process improvement project.
